ROPLASS is currently pursuing its DCSBD technology that promises to solve some of the major challenges in different industrial branches.
DCSBD technology is capable to create a thin layer of macroscopically uniform high-density plasma. Already successfully conducted industrial tests have revealed following unique properties of our DCSBD plasma technology that clearly differentiate it from other plasma technologies:
- Homogeneity of DCSBD plasma increases with the discharge power density
- The power density of thin diffuse DCSBD plasma layer achieves the order of 100 W/cm3
- The macroscopically uniform plasma with the high power density can be generated in any, even in strongly electron-attaching, reactive gas mixture (oxygen O2, carbon dioxide CO2, methane CH4, hydrogen H2)
- No noble gas admixtures (helium, argon) necessity to create homogeneous plasma with DCSBD technology
- DCSBD plasma is mechanically robust and safe
- DCSBD plasma is capable to meet the on-line production requirements in textile and paper industries, particularly in nonwovens industry
- Excellent durability of DCSBD plasma surface activation
DCSBD technology developed by ROPLASS is focused on both surface treatment and deposition of functional coatings. Our atmospheric plasma technology is able to treat the materials such as semiconductor, polymers, fabrics, wood, paper and others in a safe, environmentally friendly and cost-effective way. What is the DCSBD’s potential to do with treated substrates?






Excellent stability of plasma-treated polymer surfaces by roll-to-roll


The figure shows a curved DCSBD plasma unit operating under ambient air in a roll-to-roll setup with flexible polymer foils and the evolution of the water contact angle of flexible polyamide foil surfaces treated by curved DCSBD and industrial corona and stored for 14 days. Results indicate improved stability of surfaces treated by DCSBD thanks to the effects of diffuse plasma on the polymer surfaces.
Application examples
1. Flat glass cleaning and activation
DCSBD open-air plasma treatment leads to excellent wettability of glass surfaces. Plasma efficiently removes adsorbed carbon nano-contaminants and generates hydrophilic functional strongly reactive hydroxyl (–OH) groups. Higher wettability leads to better adhesion of coatings and inks on the glass surfaces.
Safety glass
The application of plasma treatment in the development of safety glass was accomplished in collaboration with POLARTHERM FLACHGLAS GmbH (Germany) and INNOVENT e.V. Technologieentwicklung (Germany). The drop-ball tests revealed profound changes in the adhesion of both side plasma treated foil inserted between two plasma-treated glasses.
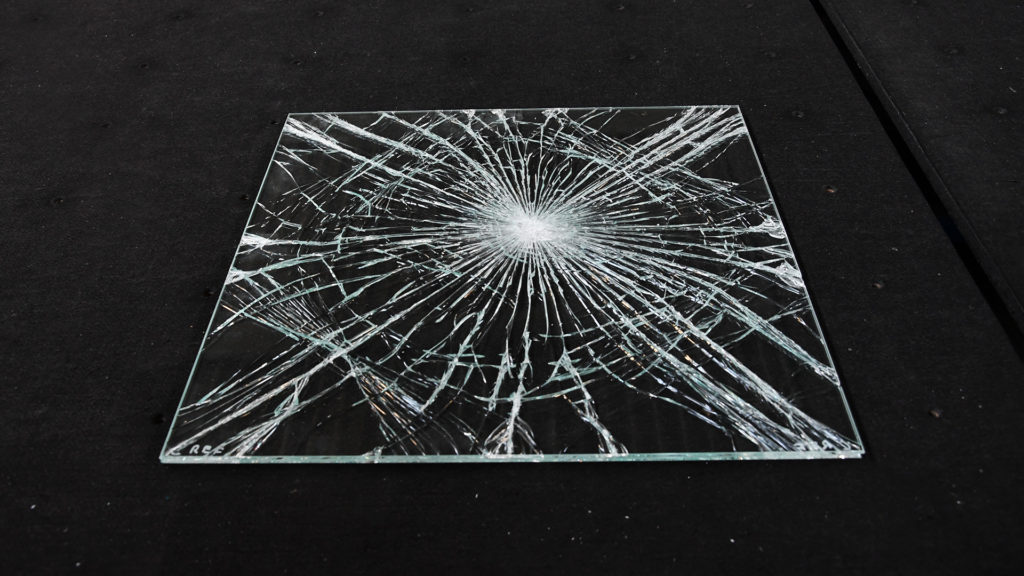
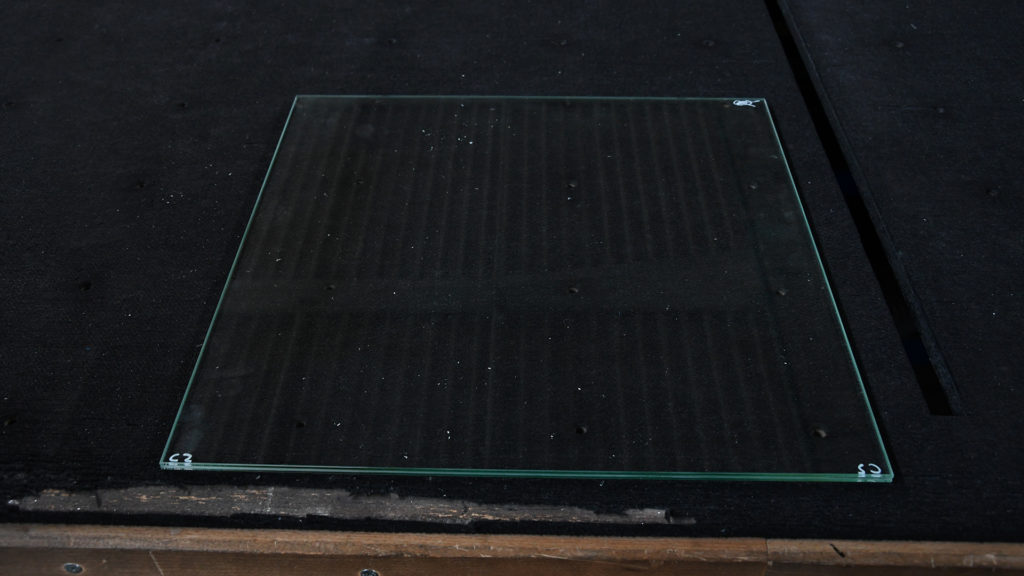
2. High-speed, low-cost activation of Polypropylene non-woven fabrics
The results of the PP-NW fabric permanent hydrophilization obtained by narrow web treater after 1 s treatment and industrial testing at the speed of 450 m/min indicated that DCSBD technology offers a simple and cost-effective solution for in-line activation of PP-NW fabrics to improve adhesion of surfactants, dyes, inks and coatings deposited in a subsequent processing step. The industrial tests were conducted in collaboration with PEGAS NONWOVENS s. r. o., Czech Republic.

3. Roll-to-roll processing of flexible materials
Rapid low-temperature (70 °C) processing of titania electron transporting layer
Functional thin films and coatings, often used in flexible and printed electronics, are usually deposited together with a base polymer or/and organic binder. Before application, the polymeric or organic binder must be removed from the coating, and this is typically achieved by high-temperature (~400 °C) sintering. However, the high-temperature sintering precludes a functional film on thermally sensitive polymeric foils that are essential for printed electronics.
High power-density and low-temperature (70 °C) DCSBD plasma treatment for 10s of seconds (up to several minutes) has a similar effect as high-temperature sintering. Recently reported research papers showed that DCSBD plasma treatment enables to manufacture of functional mesoporous photoanodes on flexible PET.
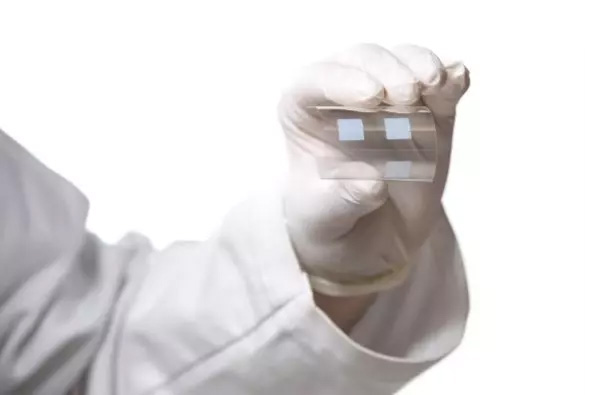
Rapid low-temperature (70 °C) reduction of nanostructured coatings
The DCSBD enables the generation of diffuse and stable plasma in hydrogen, methane, argon, and other reducing gases; at atmospheric pressure, large-area and roll-to-roll fashion.
Practical research and industrial results showed that very short hydrogen plasma treatment of graphene oxide leads to fast reduction to graphene with enhanced functional attributes. As well as graphene manufacturing, hydrogen plasma treatment enables the manufacture of silver electrodes and the synthesis of various nanoparticles.
Since the entire plasma process is at a low temperature and requires a short time, it is suitable for roll-to-roll processing and can also be utilized for printed electronics.
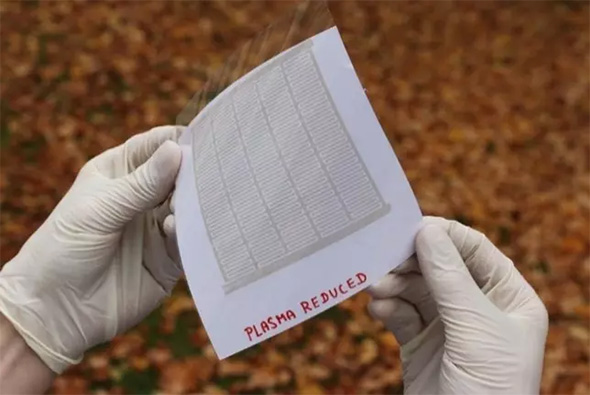
4. Low-temperature treatment of plant seeds
The short treatment time of seeds by DCSBD plasma is a prospective way for the stimulation and protection of plant seeds. The plasma can operate in humid and dusty environments in continouous regime which designates it to be adapted to industry.

The figure adopted from Plasma Chem. Plasma Process. 36 (2016) 397–414 shows the effect of growth inhibition of Fusarium Nivale on wheat seeds after 3-days of incubation.